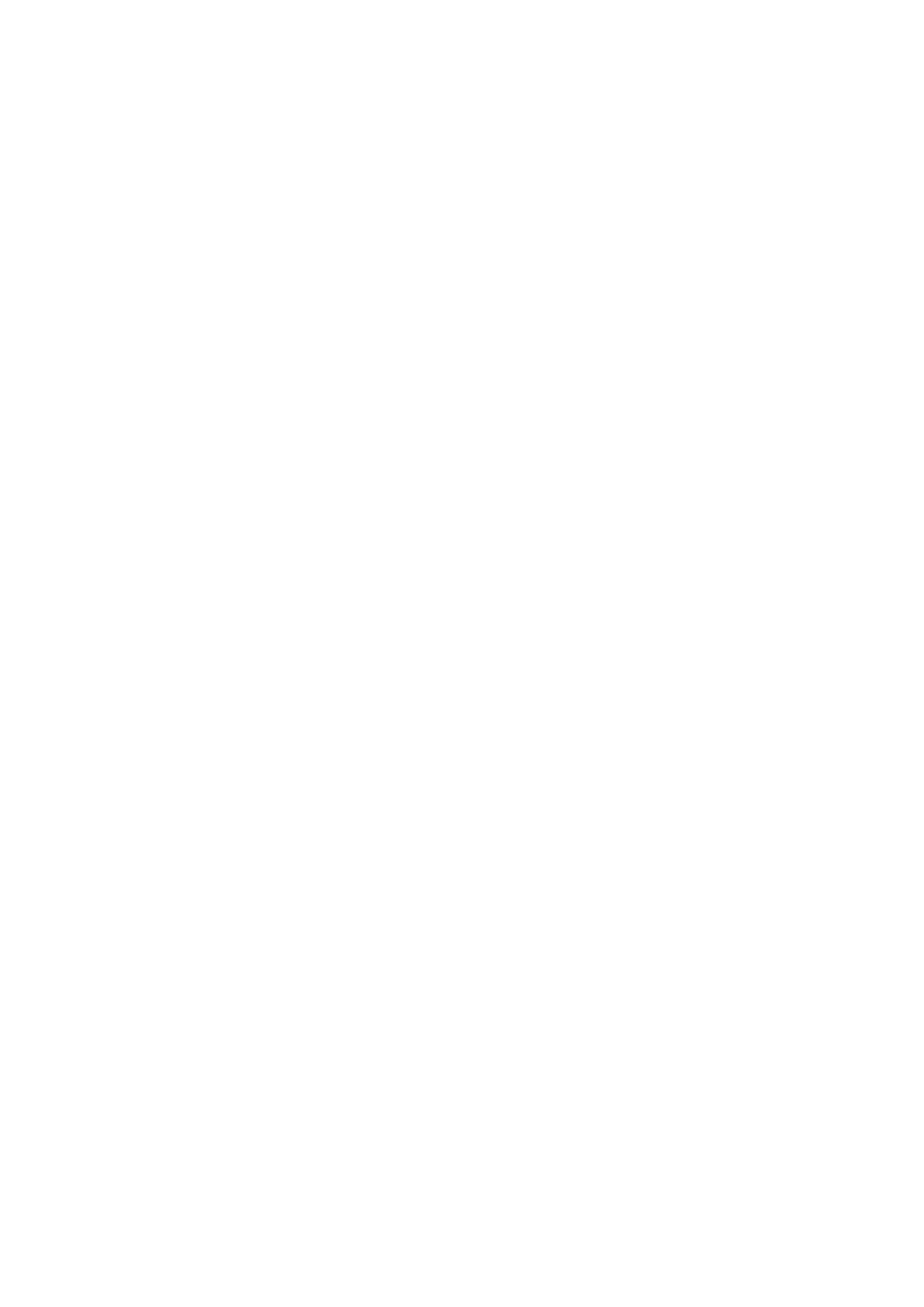
5.2 MINIMUM UND MAXIMUM FETTFÜLLSTANDANZEIGE
Die Standard Fettpumpen haben zwei Arten von Überwachungen:
Kapazitiver Mindestfüllstandschalter (für 10 und 30 Kg Behälter);
Optische Maximalfüllstandanzeige (Schwimmer).
Sie können einen Laser als Alternative installieren.
Mindest- und Maximalfüllstand Schwimmschalter ist in der Ölversion enthalten.
5.2.1 Kapazitiver Mindestfüllstandschalter (Fett)
Der Mindestfüllstand wird durch eine kapazitive Sonde, die am Ende der Leitung auf dem Behälterdeckel montiert ist, ermittelt
Wenn der Mindestfüllstand erreicht ist, zeigt die Sonde den Mangel an Schmierstoff durch ein Signal an. Falls die kapazitive
Sonde ersetzt werden muss, muss die neue Sonde kalibriert werden (siehe hierzu Kapitel 7.2 in diesem Handbuch).
5.2.2 Optische Maximalfüllstandanzeige (Fett)
Das Füllen des Behälters mit Schmiermittel wird durch den Nutzer durchgeführt.
Sobald der maximale Füllstand erreicht ist, wird durch eine kleine Stange anzeigt, dass der Behälter voll ist.
5.2.3 Laser Anzeige (Öl und Fett)
Innerhalb der Ex d kit Außenschicht, gibt es eine Lasersonde mit einem Stecker.
Sie verfügt über einen 4-stelligen alphanumerischen Display und eine Lesereichweite bis zu 10m.
Das Gerät verfügt über Programmiertasten.
5.2.4 Mindest- und Maximalfüllstandanzeige mit Schwimmer (Öl)
Der Füllstand wird durch zwei Schwimmern am Ende der Metallwelle angezeigt. Der untere Schwimmer dient als
Mindestfüllanzeige, durch Schließen eines Kontaktes, wenn der Mindestfüllstand erreicht ist. Der obere Schwimmer dient als
Maximalfüllstandanzeige, durch Schließen eines Kontaktes, wenn der Maximalfüllstand erreicht ist.
5.3 RÜHRFLÜGEL FÜR FETT
Es sind zwei Behälter mit je 10 und 30 Kg, jeweils für Öl und Fett vorgesehen.
Die Behälter sind serienmäßig mit einem Rührflügel und einem Abstreifer ausgestattet, die nicht bei der Montage oder einem
Austausch demontiert werden müssen. Unter dem Rührflügel befindet sich serienmäßig ein elektrolytisch verzinktes
Stahlgewebe mit 0,5mm Löchern. Auf dieser Weise ist die Pumpe vor Fremdkörpern, die versehentlich während des
Füllvorgangs eindringen können, geschützt.
5.4 MANOMETER
Das Manometer ist Glycerin gefüllt. So ist es vor allen Druckspitzen, die Schäden verursachen können, geschützt. Es wird direkt
in die Verteilergruppe montiert (auf der Pumpenvorderseite platziert).
5.5 BY-PASS
Der Betriebsdruck ist auf 300 bar eingestellt, ist aber einstellbar von 0 bis 380 bar.
5.6 ELEKTRISCHE ANSCHLÜSSE
Auf der Basisplatte kann eine Sicherheitsklemmbox montiert werden, die eine Klemmleiste enthält, um die elektrischen
Komponenten der Mini-SUMO Atex Pumpe (Motor, Ventile, Füllstandanzeige, Indikator, etc.) zu verbinden.
Haben Sie hierfür entschieden, wird die Pumpe bereits mit entsprechender Verdrahtung an der Klemmleiste geliefert.