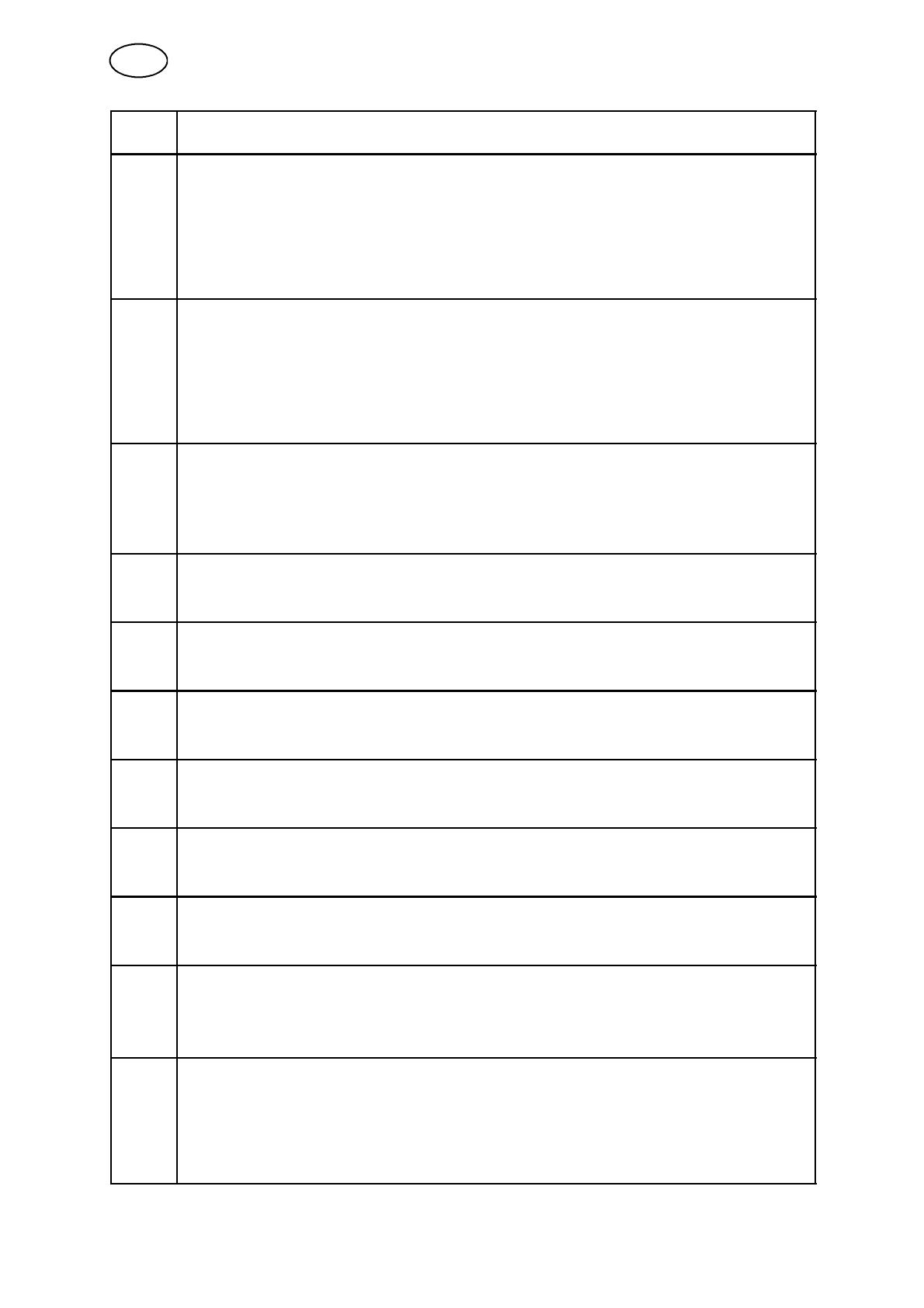
-- 1 8 --
bi02d1ga
Fehler-
code
Beschreibung
5 Mittelspannung überschreitet den Grenzwert
Die Spannung ist zu hoch oder zu niedrig. Eine zu hohe Spannung kann durch starke
Übersteuerungen im Netz oder ein zu schwaches Netz (hohe Netzdrosselung oder Verlust
einer Phase) hervorgerufen werden.
Die Stromquelle wird angehalten und ein Neustart blockiert.
Maßnahme: Trennen Sie zum Zurücksetzen die Spannungszufuhr. Wenn der Fehler wei-
terhin besteht, setzen Sie sich mit dem Wartungspersonal in Verbindung.
6 Temperatur zu hoch
Der Thermostat wurde aktiviert.
Der laufende Schweißprozess wird angehalten. Ein erneuter Start ist erst möglich, nach-
dem der Thermostat wieder zurückgesetzt wurde.
Maßnahme: V ergewissern Sie sich, dass der Ein-- bzw. Auslass für Kühlluft nicht blockiert
oder verschmutzt ist. Kontrollieren Sie ebenfalls den Arbeitszyklus. Die Nennwerte dürfen
nicht überschritten werden.
8 Niedrige Batteriespannung +3 V (Bedienkonsole)
Zu niedrige Batteriespannung. Wenn die Batterie nicht gewechselt wird, gehen alle gespe-
icherten Daten verloren.
Durch diesen Fehler werden keine Funktionen gesperrt.
Maßnahme: Beauftragen Sie das Wartungspersonal mit dem Batteriewechsel.
8 Versorgungsspannung +15 V (Vorschubeinheit und Stromquelle)
Die Versorgungsspannung ist zu hoch oder zu niedrig.
Maßnahme: Setzen Sie sich mit dem Wartungspersonal in Verbindung.
8 Versorgungsspannung +13 V (Fernbedienung)
Die Versorgungsspannung ist zu hoch oder zu niedrig.
Maßnahme: Setzen Sie sich mit dem Wartungspersonal in Verbindung.
9 Versorgungsspannung --15 V (Stromquelle)
Die Versorgungsspannung ist zu hoch oder zu niedrig.
Maßnahme: Setzen Sie sich mit dem Wartungspersonal in Verbindung.
9 Versorgungsspannung +20 V (Vorschubeinheit)
Die Versorgungsspannung ist zu hoch oder zu niedrig.
Maßnahme: Setzen Sie sich mit dem Wartungspersonal in Verbindung.
9 Versorgungsspannung +10 V (Fernbedienung)
Die Versorgungsspannung ist zu hoch oder zu niedrig.
Maßnahme: Setzen Sie sich mit dem Wartungspersonal in Verbindung.
10 Versorgungsspannung +24 V
Die Versorgungsspannung ist zu hoch oder zu niedrig.
Maßnahme: Setzen Sie sich mit dem Wartungspersonal in Verbindung.
11 Drahtgeschwindigkeit
Die Drahtgeschwindigkeit weicht vom V orgabewert ab.
Bei Auftreten des Fehlers wird der Drahtvorschub angehalten.
Maßnahme: Setzen Sie sich mit dem Wartungspersonal in Verbindung.
12 Kommunikationsfehler (Warnung)
Die Auslastung des CAN--Systembusses ist vorübergehend zu hoch.
Möglicher Kontaktverlust zwischen Bedienkonsole und Stromquelle/V orschubeinheit.
Maßnahme: Kontrollieren Sie die Ausrüstung. Es darf lediglich eine Vorschubeinheit oder
eine Fernbedienung angeschlossen sein. Wenn der Fehler weiterhin besteht, setzen Sie
sich mit dem W artungspersonal in Verbindung.
DE