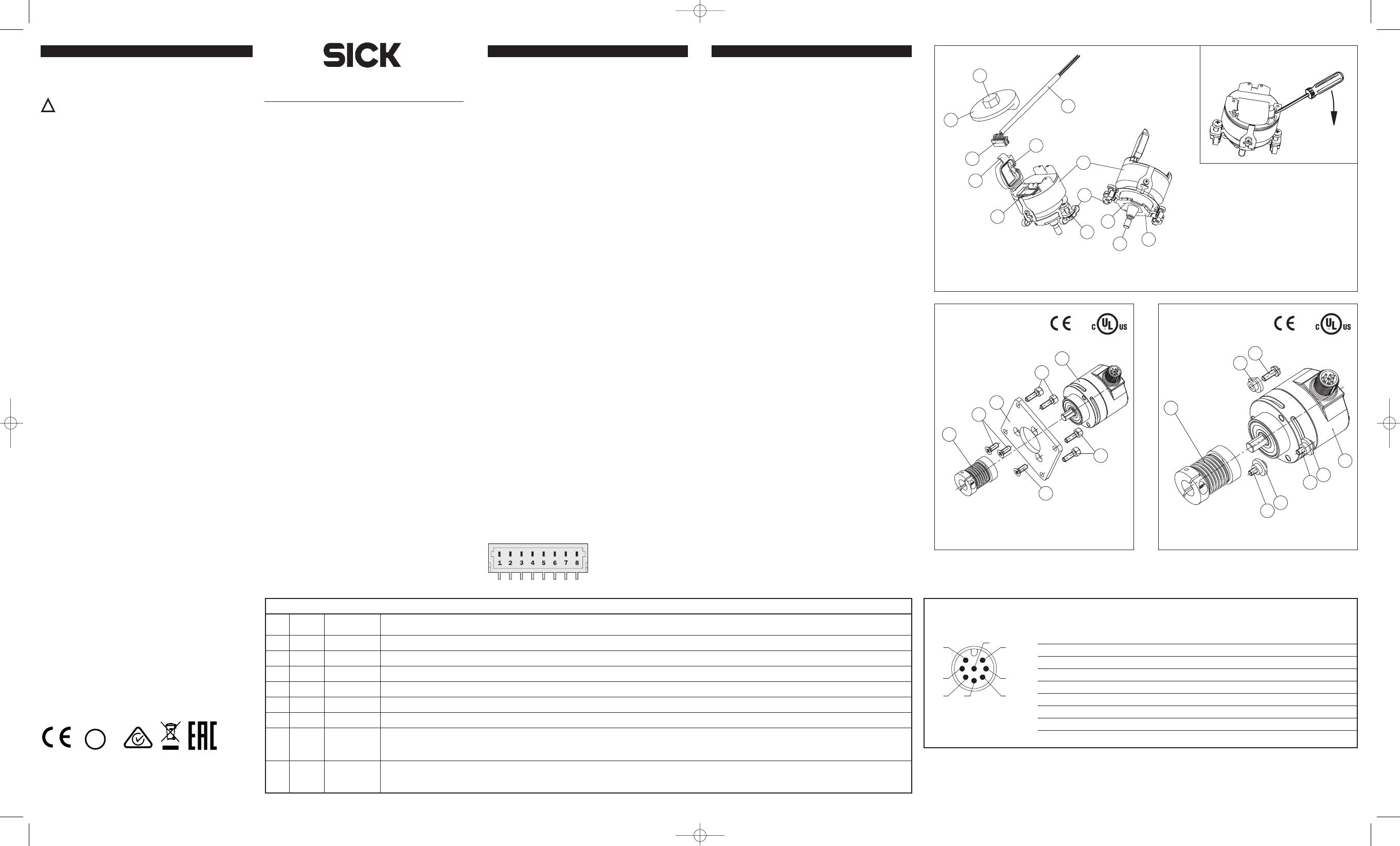
Safety Notes
Observe the professional safety regulations and accident preven-
tion regulations applicable to your country.
Switch off the voltage for all devices/machines and systems affec-
ted by the assembly.
Impacts and shocks to the shaft MUST be avoided, as this may
lead to damage to the ball bearings.
Use suitable flexible shaft couplings for stand alone encoders. The
suitability of the coupling depends on the occurring angle and
shaft offset, acceleration, temperature, speed and bearing load
permitted for the motor feedback system, as stipulated by the
motor feedback system datasheet.
Never make or undo electrical connections to the motor feedback
system when voltage is applied, otherwise this may result in
damage to the devices.
For SKS36/SKM36 encoders with tapered shaft the shaft end of
the motor may only have a diameter of 12 mm max..
Preparation for Attachment
Degrease the drive shaft and the shaft of the motor feedback
system.
Tools/Parts Required
SKS36/SKM36 STANDALONE
Mounting using the threaded flange holes requires M4 screws.
The length as well as the screw head type will depend on the fitting
conditions. Fixing via the servo groove requires servo clamps and M3
screws; select the screw length according to the fitting conditions.
SKS36/SKM36 with tapered shaft
For the mounting resp. demounting the assembly tool BEF-MW-
SKX36 is required.
Generally Applicable No tes
Using the torque support for the motor feedback system, the housing
must be correctly seated in the customer‘s flange arrangement.
The more precise the centring for the motor feedback system, the
less the angle and shaft offset during assembly and the less load on
the bearings of the motor feedback system.
EMC considerations make it mandatory to connect the housing and
the encoder, resp., to earth. For the SKS36/SKM36 with tapered
shaft, this is provided by the torque support.
For standalone motor feedback systems with a connector exit, the
connector housing is connected to the device housing so as to be
electrically conductive while, for devices with outgoing cable, the
screening and the woven screen, resp., will be connected to the
device housing.
EMC considerations make it mandatory to connect the device hou-
sing and the cable screen, resp., to earth. This may be effected via
the housing of the mating connector and by connecting the braided
screen of the cable, resp. The braided screen should be connected
over a large area.
To ensure trouble-free operation, it is imperative to ensure a clean
screen connection on both sides.
ENGLISH
SICK Motor feedback systems
Operating instructions
!
SICK Motor feedback systems
SKS36, SKM36
SKS36 STANDALONE
SKM36 STANDALONE
SICK STEGMANN GmbH
PO Box 1560 · D-78156 Donaueschingen, Germany
Dürrheimer Straße 36 · D-78166 Donaueschingen,
Germany Phone: +49 771 80 70 · Fax: +49 771 80 71 00
Subject to change without notice
ENGLISH
Motor Feedback System with
Tapered Shaft and Spring Mounting
Support (Fig. 1)
Assembly
Block customer‘s drive shaft to prevent rotation.
The hexagonal part (1) of the encoder shaft (2) must be engaged
in the recess of the fixing plate (3) of the torque support (4).
Place the assembly tool (5) on the back of the encoder and enga-
ge on the cut-outs of the encoder housing (6). Using the hexago-
nal part (7) of the assembly tool (5), screw the encoder into the
drive shaft.
Screws (8) must not hook into the fixing holes of the motor.
Tightening torque: 4 Nm + 0,8 Nm.
Release the drive shaft and rotate the encoder until the holes in
the fixing plate (3) are positioned over the fixing holes of the
motor flange. Alternately tighten the fixing plate (3) with 2 M3
screws (8) on the motor flange. This releases the encoder shaft.
Tightening torque: O,8 Nm ± 0,08 Nm.
Attention!
The internal thread in the motor shaft must be free from burrs
and dirt.
The taper must be free of dirt and grease.
Max. torque for the thread, before the taper is seated: 0,8 Nm.
Electrical connection
If neccessary please open the cover (12) with a screwdriver (Fig.
A). Engage the connector (9) fitted with the set of strands(10),
volt-free, in the connector socket (11) of the encoder. Close the
cover (12) (engage in the recess of the encoder housing). The
engagement by clicking must be clearly felt or heard.
Disassembly
Block customer’s drive shaft to prevent rotation.
If neccessary please open the cover (12) with a screwdriver
(Fig. A). Remove the connector fitted with the set of strands
(9+10) volt-free. Remove the 2 M3 screws (8). The fixing plate (3)
is to be positioned in such a way that the screw holes are aligned
with the stator coupling (4). Turn the encoder by hand until fixing
plate engages. Place the assembly tool (5) on the back of the
encoder and engage in the recesses of the encoder housing (6).
Using the hexagonal part (7) of the assembly tool (5), detach and
remove the encoder from drive shaft.
ENGLISH
Motor Feedback System with
Ser vo-/Face Mount Flange
(Standalone)
Assembly with mounting plate (Fig. 2)
Block customer’s drive shaft to prevent rotation.
Mount coupling (5) onto the encoder (1). Ensure that it does not
brush against the encoder flange.
Fit the encoder with 3 M4 screws (3), e.g. on the mounting plate
(2). Push encoder (1) with mounted coupling (5) and mounting
plate (2) onto drive shaft and centring/clamping neck.
Then fix the encoder (1) via 4 screws (4). Secure the screws
against loosening. Fix coupling (5) onto the drive shaft.
Screw on connector volt-free and connect strands of the
outgoing lead (volt-free), resp.
Disassembly
Block customer’s drive shaft to prevent rotation.
Undo electrical connection volt-free. Loosen coupling (5) on the
drive shaft. Undo the 4 screws (4) and remove the encoder.
Remove the fixing plate (2) by undoing the 3 screws (3) and also
remove the coupling (5) from the encoder.
Assembly with servo clamps (Fig. 3)
Block customer’s drive shaft to prevent rotation.
Mount coupling (2) on the encoder (1). Ensure that the coupling
(2) does not brush against the encoder flange. Push encoder (1)
with mounted coupling (2) onto the drive shaft and centring neck.
Mount servo clamps (3) with M3 screws (4). Tighten screws (4)
only lightly such that the encoder (1) can still be rotated.
Determine the connector position by rotating the housing. Fully
tighten to prevent screws (4) from working loose. Fix coupling (2)
onto the drive shaft.
Screw on connector volt-free and connect strands of the
outgoing lead (volt-free), resp.
Disassembly
Block customer’s drive shaft to prevent rotation.
Undo electrical connection volt-free. Remove servo clamps (3) by
undoing the screws (4). Loosen coupling (2) on the drive shaft
and detach centring neck. Remove encoder (1).
PIN and wire allocation SKS36/SKM36
PIN Signal Cable coulours Description
(Cable outlet)
1U
s
red Encoder supply voltage. The operating voltage at the encoder ranges from + 7 V to + 12 V. The recommended supply voltage is + 8 V.
2 + SIN white Process data channel; + SIN is a sine signal of 1 V
pp
with a static offset of REFSIN.
3 REFSIN brown Process data channel; a static voltage of + 2.5 V, which serves as reference voltage for + SIN.
4 + COS pink Process data channel; + COS is a cosine signal of 1 V
pp
with a static offset of REFCOS.
5 REFCOS black Process data channel; a static voltage of + 2.5 V, which serves as reference voltage for + COS.
6 GND blue Encoder ground connection; galvanically separated from the housing. The voltage relating to GND is + U
s
.
7 Data + grey or yellow Parameter channel; positive data signal. The parameter channel is an asynchronous, half-duplex interface, which physically corresponds to the EIA RS485 specification.
For this, data can be requested from the encoder through different commands; this also makes it possible to write user-specific data such as position offset to the
EEPROM of the encoder.
8 Data – green or purple Parameter channel; negative data signal. The parameter channel is an asynchronous, half-duplex interface, which physically corresponds to the EIA RS485 specification.
For this, data can be requested from the encoder through different commands; this also makes it possible to write user-specific data such as position offset to the
EEPROM of the encoder.
13
11
8
4
1
2
3
6
12
10
7
5
9
Disassembly (Fig. A)
5
2
3
3
4
4
1
Fig. 1
Fig. 2
PIN and wire allocation SKS36 STANDALONE/SKM36 STANDALONE
PIN Signal Colour of wires Explanation
1 REFSIN brown Process data channel
2 + SIN white Process data channel
3 REFCOS black Process data channel
4 + COS pink Process data channel
5 Daten + grey or yellow RS-485 Parameter channel
6 Daten – green or purple RS-485 Parameter channel
7 GND blue Ground connection
8 +U
s
red Encoder Supply voltage
Screen Housing potential
View of the plug-in face
2
3
4
4
3
3
4
1
Fig. 3
12
3
7
8
8-pin A coded
For use in NFPA 79 applications only.
Interconnection cables and accessories
are available from Sick.
C US
U
L
®
MA_SKS-M36:MA_SKS/M36 22.03.2011 10:25 Uhr Seite 2
8013452/13AP/2019-03-27 · AB_07
BZ int48
Please find detailed addresses and further locations in all major industrial
nations at www.sick.com
Australia
Phone +61 (3) 9457 0600
Austria
Phone +43 (0) 2236 62288-0
Belgium/Luxembourg
Phone +32 (0) 2 466 55 66
Brazil
Phone +55 11 3215-4900
Canada
Phone +1 905.771.1444
Czech Republic
Phone +420 2 57 91 18 50
Chile
Phone +56 (2) 2274 7430
China
Phone +86 20 2882 3600
Denmark
Phone +45 45 82 64 00
Finland
Phone +358-9-25 15 800
France
Phone +33 1 64 62 35 00
Germany
Phone +49 (0) 2 11 53 01
Hong Kong
Phone +852 2153 6300
Hungary
Phone +36 1 371 2680
India
Phone +91-22-6119 8900
Israel
Phone +972-4-6881000
Italy
Phone +39 02 27 43 41
Japan
Phone +81 3 5309 2112
Malaysia
Phone +603-8080 7425
Mexico
Phone +52 (472) 748 9451
Netherlands
Phone +31 (0) 30 229 25 44
New Zealand
Phone +64 9 415 0459
Norway
Phone +47 67 81 50 00
Poland
Phone +48 22 539 41 00
Romania
Phone +40 356-17 11 20
Russia
Phone +7 495 283 09 90
Singapore
Phone +65 6744 3732
Slovakia
Phone +421 482 901 201
Slovenia
Phone +386 591 78849
South Africa
Phone +27 (0)11 472 3733
South Korea
Phone +82 2 786 6321
Spain
Phone +34 93 480 31 00
Sweden
Phone +46 10 110 10 00
Switzerland
Phone +41 41 619 29 39
Taiwan
Phone +886-2-2375-6288
Thailand
Phone +66 2 645 0009
Turkey
Phone +90 (216) 528 50 00
United Arab Emirates
Phone +971 (0) 4 88 65 878
United Kingdom
Phone +44 (0)17278 31121
USA
Phone +1 800.325.7425
Vietnam
Phone +65 6744 3732