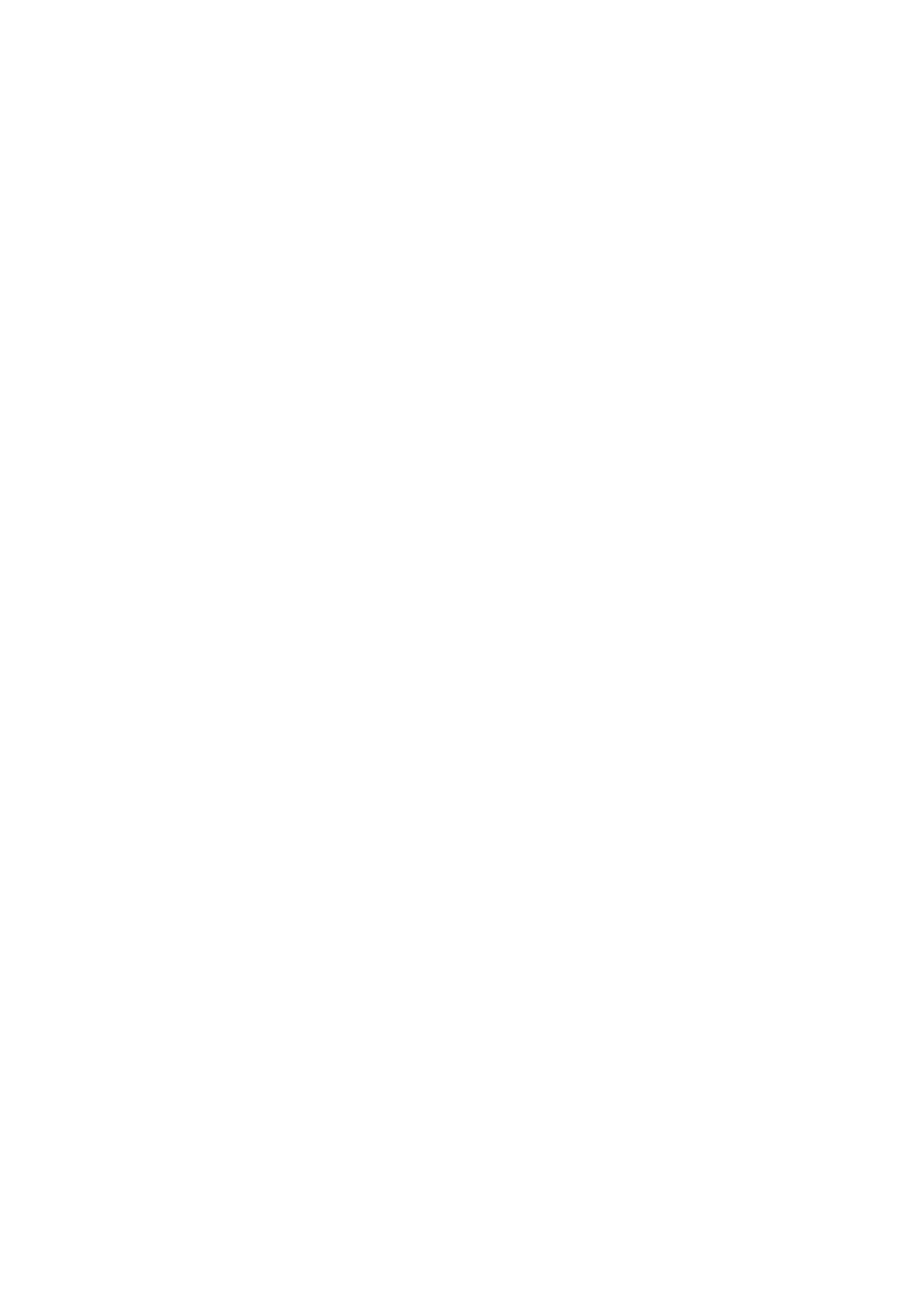
-- 3 --
TOCg
Änderungen vorbehalten.
1 SICHERHEIT 4.......................................................
2 EINLEITUNG 6.......................................................
2.1 Allgemein 6................................................................
2.2 Schweißmethode 6..........................................................
2.3 Definitionen 6...............................................................
2.4 Technische Daten 7.........................................................
2.5 Hauptbauteile -- A2 SF (UP) 8................................................
2.6 Hauptbauteile -- A2 SF (UP, T win) 8...........................................
2.7 Hauptbauteile -- A2 SG (MIG/MAG) 9..........................................
2.8 Hauptbauteile -- A2 SG 4WD (MIG/MAG) 9.....................................
2.9 Beschreibung der Hauptbauteile 10.............................................
3 INSTALLATION 11....................................................
3.1 Allgemeines 11..............................................................
3.2 Montage 11.................................................................
3.3 Einstellung des Bremsnabe 12.................................................
3.4 Anschlüsse 13...............................................................
4 BETRIEB 16..........................................................
4.1 Allgemein 16................................................................
4.2 Laden des Schweißdrahts (A2 SF, A2 SG) 17....................................
4.3 Laden des Schweißdrahts (A2 SG 4 WD) 19.....................................
4.4 Auswechseln der V orschubrolle (A2 SF, A2 SG) 20...............................
4.5 Auswechseln der V orschubrolle (A2 SG 4WD) 20.................................
4.6 Kontaktausrüstungen für UP--Schweißen 21.....................................
4.7 Kontaktausrüstungen für MIG/MAG--Schweißen 22...............................
4.8 Einfüllen von Schweißpulver (UP--Schweißen) 24.................................
4.9 Umbau von A2 SF (UP--Schweißen) für MIG/MAG--Schweißen 24..................
4.10 Umbau von A2 SF (UP--Schweißen) für Twinarc 24...............................
5 WARTUNG 25........................................................
5.1 Allgemein 25................................................................
5.2 Täglich 25...................................................................
5.3 Regelmäßig 25..............................................................
6 FEHLERSUCHE 26....................................................
6.1 Allgemein 26................................................................
6.2 Mögliche fehler 26............................................................
7 ZUBEHÖR 27.........................................................
8 ERSATZTEILBESTELLUNG 27.........................................
MASSBILD 28.........................................................
ERSATZTEILLISTE 35....................................................