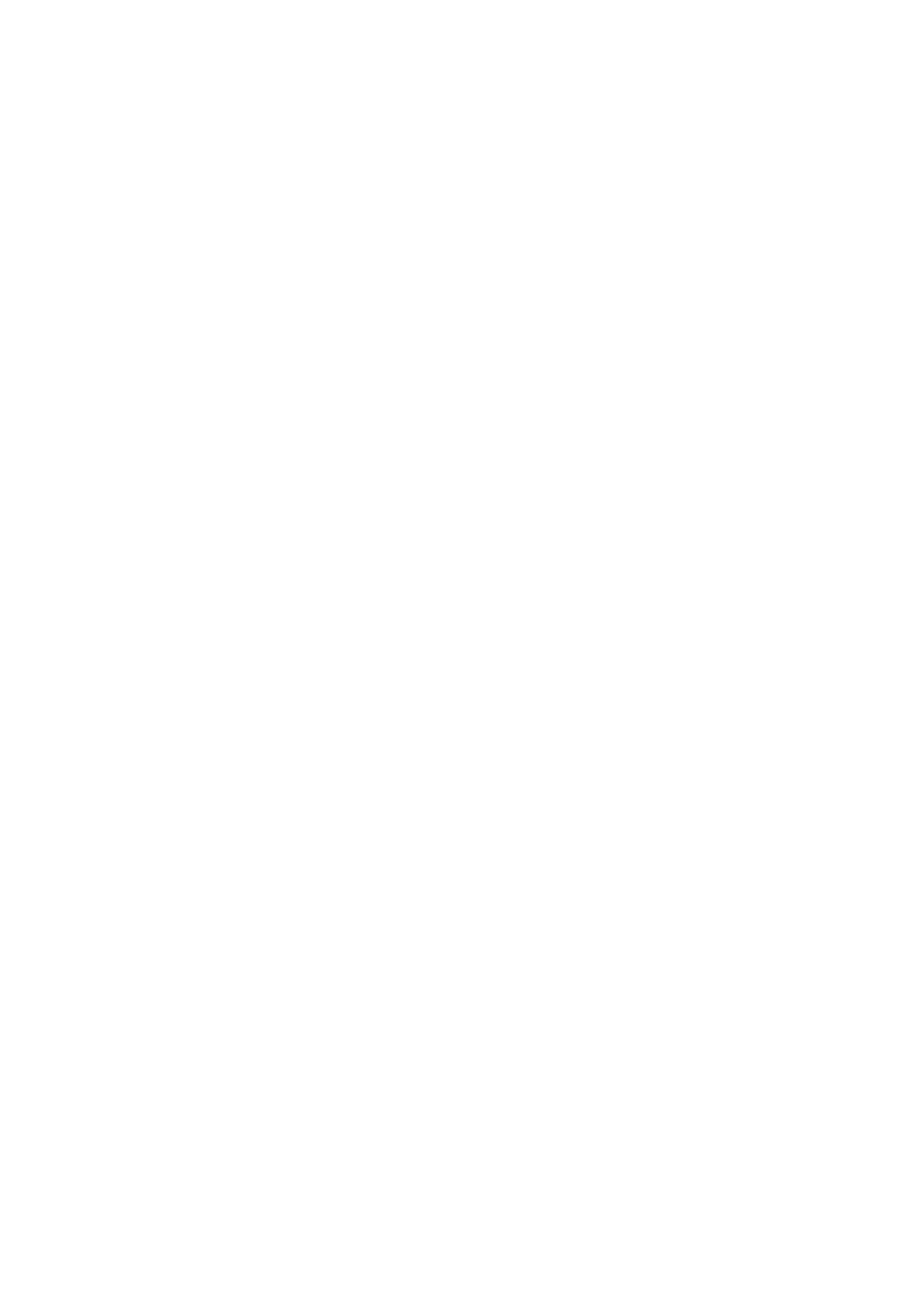
DK – INDHOLDSFORTEGNELSE - Advarsel / Elektromagnetisk støjudstråling...................................................................................... 5
- Maskinprogram / Hvad er plasmaskæring....................................................................................... 6
- Ibrugtagning ..................................................................................................................................... 6
- Betjeningsvejledning ........................................................................................................................ 8
- Vedligeholdelse .............................................................................................................................. 10
- Tekniske data ................................................................................................................................. 11
- Garantibestemmelser .................................................................................................................... 12
- Kredsløbsdiagrammer ............................................................................................................ 77 - 79
- Reservedelsliste
GB – CONTENTS - Warning / Electromagnetic emissions ........................................................................................... 13
- Machine programme / What is plasma cutting .............................................................................. 14
- Initial instructions ............................................................................................................................ 14
- Control unit ..................................................................................................................................... 16
- Maintenance .................................................................................................................................. 18
- Technical data ................................................................................................................................ 19
Warranty regulations ...................................................................................................................... 20
- Circuit diagrams ...................................................................................................................... 77 - 79
- Spare parts list
D – INHALTSVERZEICHNIS - Warnung / Elektromagnetische Störungen.................................................................................... 21
- Produktübersicht / Was ist Plasmaschneiden ............................................................................... 22
- Anschluß und Inbetriebnahme ....................................................................................................... 22
- Kontrolleinheit ................................................................................................................................ 24
- Wartung ......................................................................................................................................... 26
- Technische Daten .......................................................................................................................... 27
- Garantiebedingungen .................................................................................................................... 28
- Koppeldiagramme ................................................................................................................... 77 - 79
- Ersatzteilliste
F – TABLE DES MATIERES - Avertissement / Emissions électromagnétiques ............................................................................ 29
- Programme de la machine / Définition de la découpe au plasma ................................................ 30
- Instructions préalables ................................................................................................................... 30
- Unité de commande ....................................................................................................................... 32
- Maintenance .................................................................................................................................. 34
- Caractéristiques techniques .......................................................................................................... 35
Garantie ......................................................................................................................................... 36
- Schémas de connexion .......................................................................................................... 77 - 79
- Liste des pièces de rechange
SE – INNEHÅLLSFÖRTECKNING - Varning / Elektromagnetisk störfält ................................................................................................ 37
- Maskinprogram / Vad är plasmaskärning ...................................................................................... 38
- Igångsättning ................................................................................................................................. 38
- Funktionsvägledning ...................................................................................................................... 40
- Underhåll ........................................................................................................................................ 42
- Teknisk data ................................................................................................................................... 43
- Garantibestämmelser .................................................................................................................... 44
- Kretsloppsdiagram .................................................................................................................. 77 - 79
- Reservdelslista
FI – SISÄLLYSLUETTELO - Varoitus / Sähkömagneettiset häiriöt ............................................................................................. 45
- Tuoteohjelma / Mitä plasmaleikkaus on ........................................................................................ 46
- Käyttöönotto ................................................................................................................................... 46
- Ohjausyksikkö ................................................................................................................................ 48
- Huolto ............................................................................................................................................. 50
- Tekniset tiedot ................................................................................................................................ 51
- Takuuehdot .................................................................................................................................... 52
- Kytkentäkaavio ........................................................................................................................ 77 - 79
- Varaosaluettelo
I – INDICE - Attenzione / Emissioni elettromagnetiche...................................................................................... 53
- Gamma / Cos’e’ il taglio plasma? .................................................................................................. 54
- Istruzioni iniziali .............................................................................................................................. 54
- Pannello di controllo ....................................................................................................................... 56
- Manutenzione ................................................................................................................................ 58
- Dati tecnici ...................................................................................................................................... 59
- Condizioni di garanzia ................................................................................................................... 60
- Schema elettrico ..................................................................................................................... 77 - 79
- Lista parti di ricambio
NL – INHOUD - Waarschuwing / Elektromagnetische emissie ............................................................................... 61
- Machineprogramma / Wat is plasmasnijden ................................................................................. 62
- Aan de slag .................................................................................................................................... 62
- Besturingsunit ................................................................................................................................ 64
- Onderhoud ..................................................................................................................................... 66
- Technische gegevens .................................................................................................................... 67
- Garantievoorwaarden .................................................................................................................... 68
- Elektrisch schema ................................................................................................................... 77 - 79
- onderdelenlijst
RU – СОДЕРЖАНИЕ - Предупреждения / Электромагнитные излучения .................................................................... 69
- Программа поставки / Что такое плазменная резка ................................................................. 70
- Начало работы ............................................................................................................................. 70
- Блок управления .......................................................................................................................... 72
-
Техническое обслуживание ........................................................................................................ 74
- Технические данные .................................................................................................................... 75
- Условия гарантии ......................................................................................................................... 76
- Схемы цепи ........................................................................................................................... 77 - 79
- Список запасных деталей