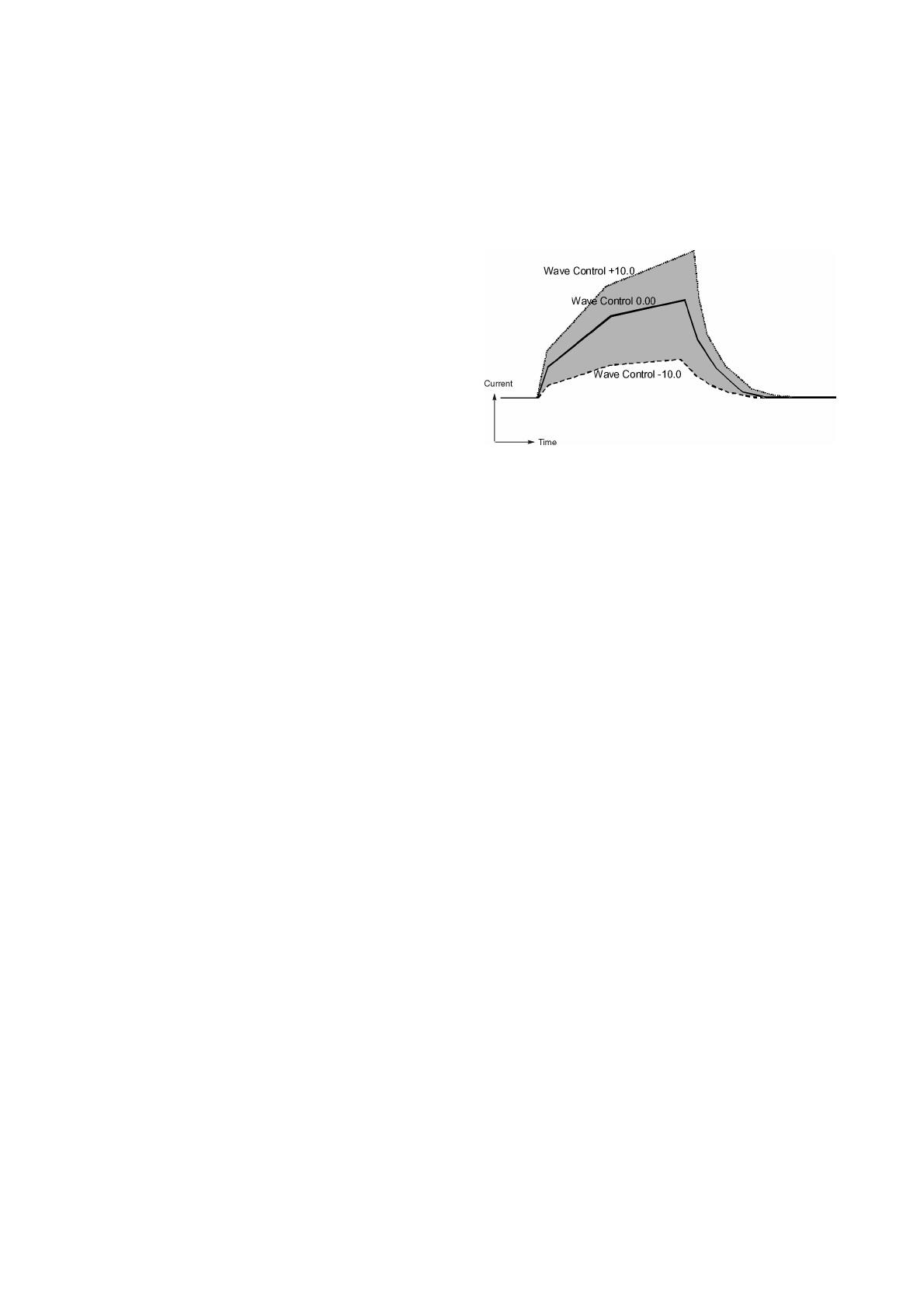
32
Bedienungsanleitung des Drahtvorschubgerätes.
WFS / AMPS:
In den synergischen Modi (synergisch CV, Impuls
GMAW, STT) WFS (Wire Feed Speed –
Drahtgeschwindigkeit) ist der führende Steuerparameter,
der alle anderen Variablen kontrolliert. Der Bediener
stellt die WFS ein, passend zu den Faktoren, wie Naht-
Abmessungen, Einbrandforderungen, Wärme-
einbringung usw. Die Power Wave benutzt die WFS-
Einstellung zur Anpassung der Leistungseigenschaften
(Ausgangsspannung, Ausgangsstrom) übereinstimmend
mit den vorprogrammierten Einstellungen der Power
Wave. In nicht-synergischen Modi verhält sich die WFS-
Steuerung als eine konventionelle CV-Stromquelle, wo
WFS und Spannung unabhängige Einstellungen sind.
Der Bediener muss daher die Spannung anpassen an
Änderungen im WFS, um die Lichtbogeneigenschaften
beizubehalten.
In Konstantstrom-Modi (Elektrode, WIG) passt diese
Steuerung den Ausgangsstrom an.
Spannung:
In Konstantspannungs-Modi (Syneric CV, Standard CV)
passt die Steuerung die Schweißspannung an.
In Impulssynergischen Modi (nur Impuls-GMAW) kann
der Bediener die Trim-Einstellung ändern, um die
Lichtbogenlänge anzupassen. Es ist einstellbar von
0.500 bis 1500. Eine Trim-Einstellung von 1000 ist eine
gute Ausgangsposition.
Nur 455M/STT: Im STT Modus kann der Bediener die
Trim-Einstellung anpassen, um die generelle
Wärmeeinbringung in der Schweißnaht zu ändern.
Schweiß-Modus:
Dieser kann nach Namen gewählt werden (CV MIG, CC
Elektrode, Fugen usw.) oder nach Modusnummer (10,
24, 71 usw.) abhängig von den Optionen der Steuerung.
Das Wählen eines Schweißmodus legt die
Ausgangseigenschaften der Power Wave fest. Für
weitere Informationen lesen Sie die nachfolgenden
Absätze.
Lichtbogensteuerung:
Auch bekannt als Drossel oder Wave Control, erlaubt es
dem Schweißer die Lichtbogeneigenschaften in allen
Schweiß-Modi von “weich” nach “hart” zu ändern. Dies
ist einstellbar von –10.0 bis +10.0, nominelle Einstellung
ist 00.0 (nominelle Einstellung 0.00 kann auf manchen
Power Feed Displays als “OFF” angezeigt werden).
Konstant-Spannungs-Schweißen
Synergic CV:
Vom Hersteller ist softwaremäßig für jede
Drahtgeschwindigkeit eine übereinstimmende Spannung
vorprogammiert worden. Die nominelle
vorprogrammierte Spannung ist der beste Mittelwert für
eine bestimmte Drahtgeschwindigkeit, die Power Wave
stellt automatisch das Spannungsniveau ein, damit
gleichwertige Lichtbogeneigenschaften über den ganzen
WFS-Bereich beibehalten werden.
Nicht-Synergic CV:
Dieser Schweißmodus verhält sich eher wie eine
konventionelle CV-Stromquelle. Spannung und
Drahtgeschwindigkeit sind unabhängige Eigenschaften,
so dass der Bediener die Spannung anpassen muss, um
etwaige Änderungen in der WFS zu korrigieren.
Alle CV-Modi:
Die Lichtbogensteuerung auch Wave Form Control
genannt, passt die Drossel der Wave-Form an. Das
Vergrößern der Wave Form Control über 0.0 gibt einen
harten, kühleren Lichtbogen und das Verkleinern der
Wave Control unter 0.0 einen weicheren, heißeren
Lichtbogen (Siehe Abbildung unten).
Impulsschweißen
Impulsschweißen wird eingestellt durch Steuerung einer
Lichtbogenlängen-Variablen. Beim Impulsschweißen ist
die Lichtbogenspannung sehr abhängig von der Puls-
Form. Die Pulsstromstärke, die Grundstromstärke, die
Stromanstiegszeit, die Abfallzeit und die Impulsfrequenz
beeinflussen die Spannung. Die genaue Spannung für
eine bestimmte Drahtgeschwindigkeit kann nur
errechnet werden, wenn alle Impuls-Parameter bekannt
sind. Es ist unpraktisch, eine vorprogrammierte absolute
Spannung zu benutzen, daher wird die Lichtbogenlänge
eingestellt durch Anpassung der “Trim”.
Die Einstellung “Trim” stellt die Lichtbogenlänge ein und
läuft von 0.50 bis 1.50, mit einem nominellen Wert von
1.00. Trim - Werte über 1.00 vergrößern die
Lichtbogenlänge, Werte unter 1.00 verkleinern diese.
Die meisten Impulsschweiß-Programme sind synergisch.
Wenn die Drahtgeschwindigkeit eingstellt wird, wird die
Power Wave automatisch die Wave-Form-Parameter
neu berechnen um gleichwertige
Lichtbogeneigenschaften beizubehalten.
Die Power Wave benutzt “Adaptive Control" um beim
Schweißen Änderungen in der freien Drahtlänge
auszugleichen (freie Drahtlänge ist der Abstand
zwischen Kontaktdüse und Werkstück). Die Wave Form
der Power Wave ist für eine 19mm freie Drahtlänge
optimiert. Die “ Adaptive Control” unterstützt eine freie
Drahtlänge von 13 bis 32mm. Bei sehr niedrigen oder
hohen Drahtgeschwindigkeiten kann der Bereich kleiner
sein, durch die physikalische Grenze des
Schweißprozesses.
Lichtbogensteuerung, auch Wave Control genannt, stellt
bei Impulsprogrammen meistens den Fokus oder die
Form des Lichtbogens ein. Wave Control - Werte über
0.0 vergrößern die Impulsfrequenz und verkleinern den
Grundstrom. Dieser gibt einen kompakten, straffen
Lichtbogen, ausgezeichnet geeignet für Hochgeschwin-
digkeits-Blechschweißen. Wave Control – Werte unter
0.0 verkleinern die Impuls-Frequenz und vergrößern den
Grundstrom. Dies gibt einen weichen Lichtbogen,
ausgezeichnet für Schweißen in Zwangslage (Siehe
Abbildung unten).