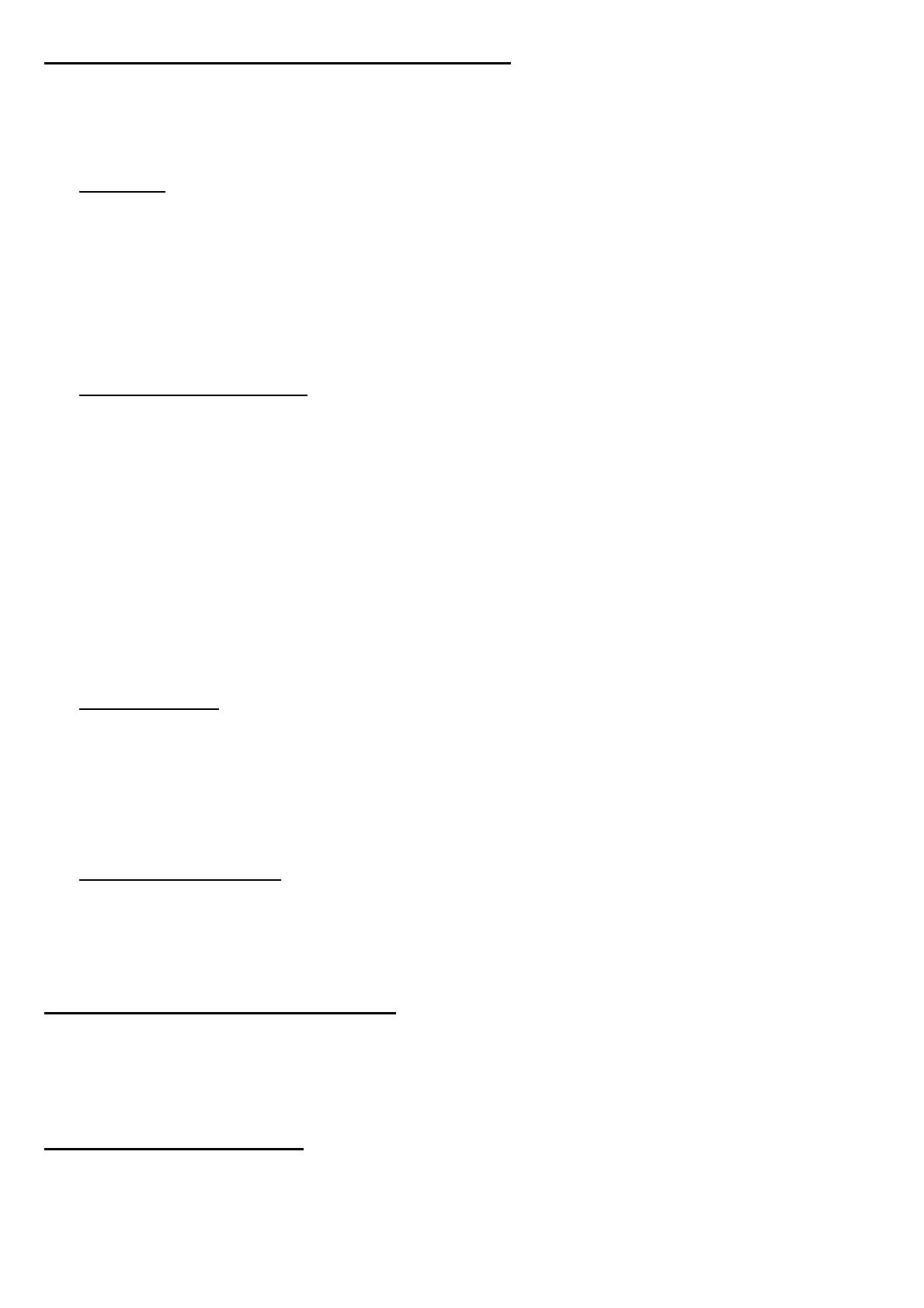
- 8 -
2. INTERPOLIERTES GEWINDESCHNEIDEN
Ab dieser Version ist es möglich, sowohl typisches Gewindeschneiden (mit Kompensator) “P630(3)=0” als auch interpoliertes
Gewindeschneiden durchzuführen.
Für das interpolierte Gewindeschneiden muß die CNC die Spindel steuern und dabei ständig die Drehgeschwindigkeit überprüfen und
dem Schaltschrank die entsprechenden Analogsignale übermitteln, damit die Spindel mit der gewählten Geschwindigkeit dreht.
Allgemeines:
Das interpolierte Gewindeschneiden basiert auf einer Interpolation zwischen Spindel und Z-Achse.
Die Beschleunigungs-/Verzögerungszeiten der Spindel und der Z-Achse sollten übereinstimmen.
Der Nachlauffehler der Spindel und der der Z-Achse sollten proportional sein. Wenn zum Beispiel mit F1000 mm/min, S1000 U/
min (Gewindesteigung =1mm) gearbeitet wird und sich Nachlauffehler von Z=1mm (Beobachtung) und S=360 Grad ergeben,
so sind beide Achsen perfekt synchronisiert.
Die Beschleunigung und Verzögerung der Spindel kann für jede Getriebestufe separat eingestellt werden, da hierfür verschiedene
Parameter vorgesehen sind.
Da die Verstärkung der Z-Achse während der Bearbeitung und während des interpolierten Gewindeschneidens nicht gleich ist,
verfügt die CNC hierfür über zwei separate Parameter.
Der Ausgang GEWINDESCHNEIDEN_ON (I97) ist immer dann aktiv, wenn ein interpoliertes Gewindeschneiden ausgeführt wird.
Maschinenparameter der Spindel:
P800 Anzahl der Spindeldrehgeberimpulse (0...9999)
P601(7) Vorzeichen des mit M19 verbundenen analogen Ausgangs (0 oder 1)
P609(2) Zählrichtung der Spindel (0 oder 1)
P612(8) Impulsart des Maschinenreferenzpunkts in der Spindel 0=negative 1=positive)
P719 Minimales Analogsignal der Spindel (0...255)
P719=0 ==> 2,5 mV P719=10 ==> 25.0 mV (10 x 2.5)
P719=1 ==> 2,5 mV P719=255 ==> 637.5 mV (255 x 2.5)
P717 Totband der Spindel. Anzahl der Zählimpulse (0...255)
Die CNC wendet intern auf die Meßsystemsignale des Drehgebers einen Multiplikationsfaktor von x4 an.
Bei einem Drehgeber von 1000 Impulsen pro Umdrehung und P717=100 ist das Totband also: (360°/4000)x100=±9°
P718 Proportionale Spindelverstärkung K (0...255)
Das entsprechende Analogsignal wird so auf 1 Nachlauffehler-Zählimpuls des Spindeldrehgebers festgelegt.
Analogsignal (mV.)=P718 X Nachlauffehler (Impulse) X 2,5 mV / 64
P751, P747, P748, P749Dauer der Beschleunigungs-/Verzögerungsrampe der Spindel in Stufe 1, 2, 3, 4 (0...255) Wert 1=20ms
P746 Vorschub-Verstärkung der Spindel beim interpolierten Gewindeschneiden (0...255)
P750 Proportionale Verstärkung K1 der Z-Achse beim interpolierten Gewindeschneiden (0...255)
P625(1) Der Beginn des Gewindes ist mit dem Spindelreferenzpunkt synchronisiert (0=nein, 1=ja)
Meßsystemeingänge:
P630(4)=0 Der Steckverbinder A5 wird für den Meßsystemeingang der Spindel und den des mit der Z-Achse verbundenen
Handrads genutzt.
Beide Meßsystemeingänge müssen extern umgeschaltet werden.
P630(4)=1 Der Steckverbinder A5 wird nur für den Meßsystemeingang der Spindel genutzt.
Der Steckverbinder A6 wird für den Meßsystemeingang des mit der X-Achse verbundenen Handrads genutzt.
Der Steckverbinder A4 wird für den Meßsystemeingang des mit der Y- und Z-Achse verbundenen Handrads (oder
Handräder) genutzt.
Programmierung in ISO-Code
Programmierung mit Hilfe der Funktion G33 (Gewindeschneiden). Hier muß der Achsvorschub und die Spindelgeschwindigkeit
angegeben werden.
Beispiele: G33 Z -10 F1000 S1000 M3 F1000 S1000 M3
G33 Z-10
Die Funktionen G00, G01, G02 und G03 heben die Funktion G33 auf.
3. SOFTWAREVERSION DER CNC
Ab dieser Version werden bei Einschalten des Bildschirms die Prüfsummen (cheksum) aller Eproms angezeigt,
[Hilfsmodi] [Sondermodi] [8]
Die CNC zeigt die Prüfsummen aller Eproms sowie die Softwareversion.Beispiel: Version 3.1
4. BILDSCHIRMSCHUTZ
Wird der Maschinenparameter “P626(7)=1” gesetzt, so funktioniert der Bildschirmschutz folgendermaßen :
Wird 5 Minuten lang keine Taste berührt und die Steuerung hat keinen Anlaß, das Bildschirmbild zu aktualisieren, so wird das
Videosignal unterdrückt und der Bildschirm schaltet sich ab. Wird eine beliebige Taste gedrückt, so schaltet er sich wieder ein.