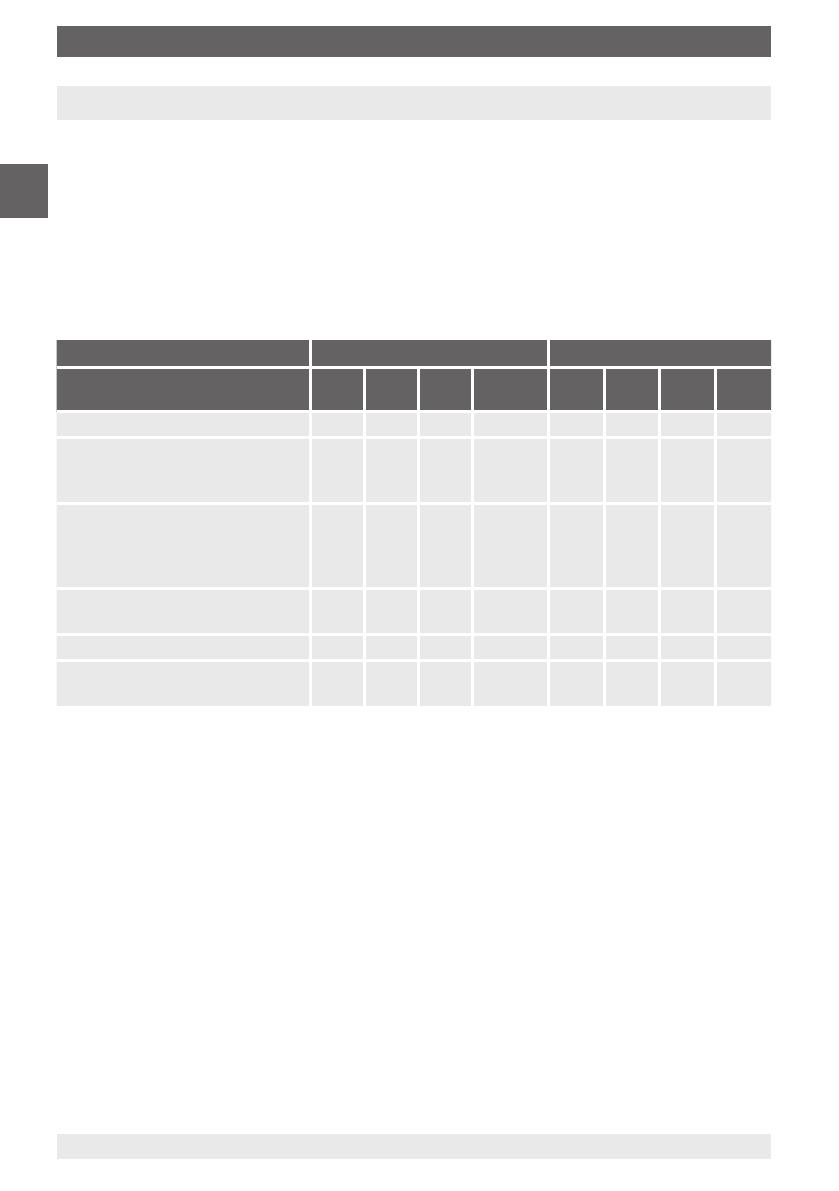
EN
14280101.01 03/2019 EN/DE/FR/ES
WIKA additional information TR12/TC12, flameproof enclosure (Ex d)18
5. Calculation examples for self-heating at the thermowell tip
The self-heating at the thermowell tip depends upon the sensor type (TC/RTD), the
measuring insert diameter and the thermowell design. The table below shows the possible
combinations. The heating at the probe tip of the bare measuring insert is clearly higher;
the representation of these values was omitted on the grounds of the required assembly
with a thermowell.
The table shows that thermocouples generate much less self-heating than resistance
thermometers.
Thermal resistance [R
th
in K/W]
Sensor type RTD TC
Measuring insert diameter
in mm
2.0 -
< 3.0
3.0 -
≤6.0
6 - 8 3.0 -
6.0 mm
5
0.5 -
< 1.5
1.5 -
< 3.0
3.0 -
< 6.0
6.0 -
12.0
Without thermowell 245 110 75 225 105 60 20 5
With fabricated thermowell
(straight and tapered), e.g. TW35,
TW40 etc.
135 60 37 - - - 11 2.5
With thermowell - solid-body
material (straight and tapered),
e.g. TW10, TW15, TW20, TW25,
TW30 etc.
50 22 16 - - - 4 1
Special thermowell
per EN 14597
- - 33 - - - - 2.5
Tx55 (retaining tube) - 110 75 225 - - 20 5
Built into a blind bore
(minimum wall thickness 5 mm)
50 22 16 45 22 13 4 1
5.1 Example calculation for variant 2 with RTD sensor
▶
Use at the partition to zone 0, marking II 1/2G Ex db IIC T1 ... T6 Ga/Gb
Power-limiting circuit using a fuse with 32 mA
Calculate the maximum possible temperature, T
max
, at the thermowell tip for the following
combination:
▶
Ø 6 mm RTD measuring insert with built-in head-mounted transmitter, assembled with
solid-machined thermowell
T
max
is obtained by adding the temperature of the medium and the self-heating. The
self-heating depends on the supplied power P
o
and the thermal resistance R
th
. The
calculated supplied power, P
o
, comes from the chosen standard value for the fuse and is
only realised at the probe tip.
5. Calculation examples for self-heating at the thermowell tip