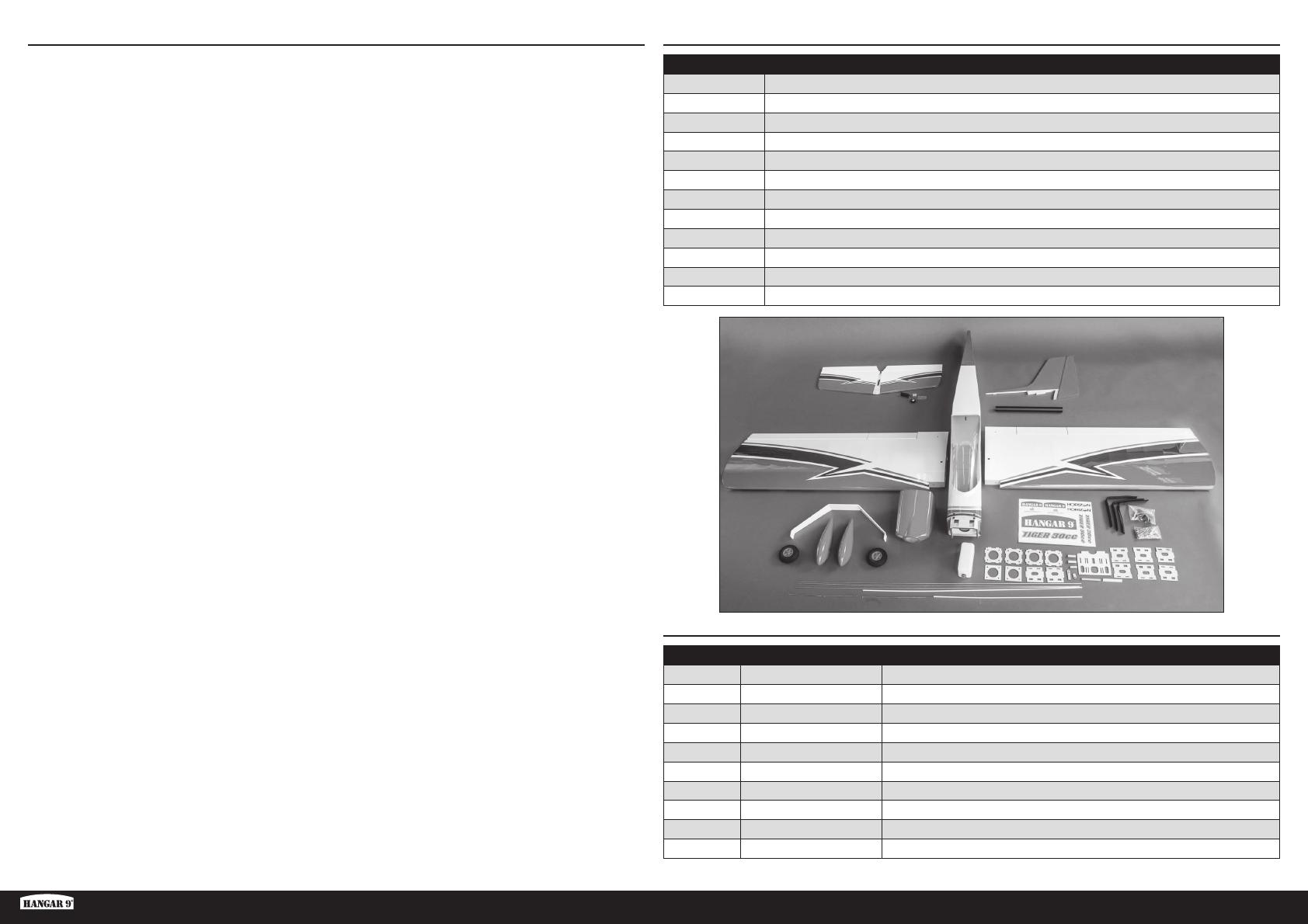
3 EN
Tiger 30cc ARF
# Required Part # Description
1 DLEG0031 DLE-30cc Gas Rear Carb w/Elec Ig &
1 EFLM4160A Power 160 BL Outrunner Motor, 245Kv
1 EFLM4180A Power 180 BL Outrunner Motor, 195Kv
1 EVOA100 Optical Ignition Kill Switch
1 GPMA1676 Float Set Avistar 30cc/EP Trainer ARF
1 GPMG4795 Rimfi re 1.60 63-62-250 Outrunner Brushless
1 HAN237013 Float Mounting Parts Set:Tiger 30cc
2 KXSB50005S30 F-Tek 5000mAh 5S 18.5V 30C, EC5
1 OSMG1533 GT33 Gas Engine
2 SPMX70006S30 7000mah 6S 22.2V Smart 30C; IC5
OPTIONAL PARTS
Part # Description
HAN237001 Fuselage
HAN237002 Wing Set
HAN237003 Tail Set
HAN237004 Cowling
HAN237005 Canopy Top Hatch
HAN237006 Wheel Pants
HAN237007 Wing Tube
HAN237008 Tailwheel Assy
HAN237009 Decal Set
HAN237010 Main Landing Gear
HAN237011 Wheels
HAN237012 Fuel Tank; 14oz
REPLACEMENT PARTSTABLE OF CONTENTS
Notice ......................................................................................................................................................................2
Meaning of Special Language ..................................................................................................................................2
Safety Warnings and Precautions .............................................................................................................................2
Safe Operating Recommendations ...........................................................................................................................2
Before Starting Assembly .........................................................................................................................................2
FAA Information .......................................................................................................................................................2
Replacement Parts ...................................................................................................................................................3
Optional Parts ..........................................................................................................................................................3
Required for Completion, All Power Options ..............................................................................................................4
Required for Completion, Gas Engine Installation......................................................................................................4
Required for Completion, Electric Motor Installation .................................................................................................4
Required Adhesives .................................................................................................................................................4
Tools Required .........................................................................................................................................................4
Removing Wrinkles ..................................................................................................................................................5
Building Precautions ................................................................................................................................................5
Transportation and Storage ......................................................................................................................................5
Replacement Covering .............................................................................................................................................5
Checking Blind Nuts.................................................................................................................................................5
For the Visually Challenged ......................................................................................................................................5
Aileron Servo Installation .........................................................................................................................................5
Flap Servo Installation (Optional) ..............................................................................................................................9
Wing and Stabilizer Installation ..............................................................................................................................10
Elevator Servo Installation ......................................................................................................................................12
Rudder and Fin Installation.....................................................................................................................................14
Rudder Servo Installation .......................................................................................................................................15
Tail Wheel Installation ............................................................................................................................................15
Main Landing Gear Installation ...............................................................................................................................16
Receiver and Receiver Battery Installation..............................................................................................................17
Electric Motor Box Assembly ..................................................................................................................................18
Electric Motor Installation .......................................................................................................................................20
Gas Engine Installation ...........................................................................................................................................22
Fuel Tank Assembly and Installation .......................................................................................................................25
Cowling and Spinner Installation ............................................................................................................................26
Center of Gravity ....................................................................................................................................................28
Control Throws ......................................................................................................................................................28
Prefl ight Checklist ..................................................................................................................................................29
Daily Flight Checks ................................................................................................................................................29
Limited Warranty ...................................................................................................................................................29
Warranty and Service Contact Information .............................................................................................................30
Instructions for Disposal of WEEE by Users in the European Union ..........................................................................30
Academy of Model Aeronautics National Model Aircraft Safety Code .......................................................................30