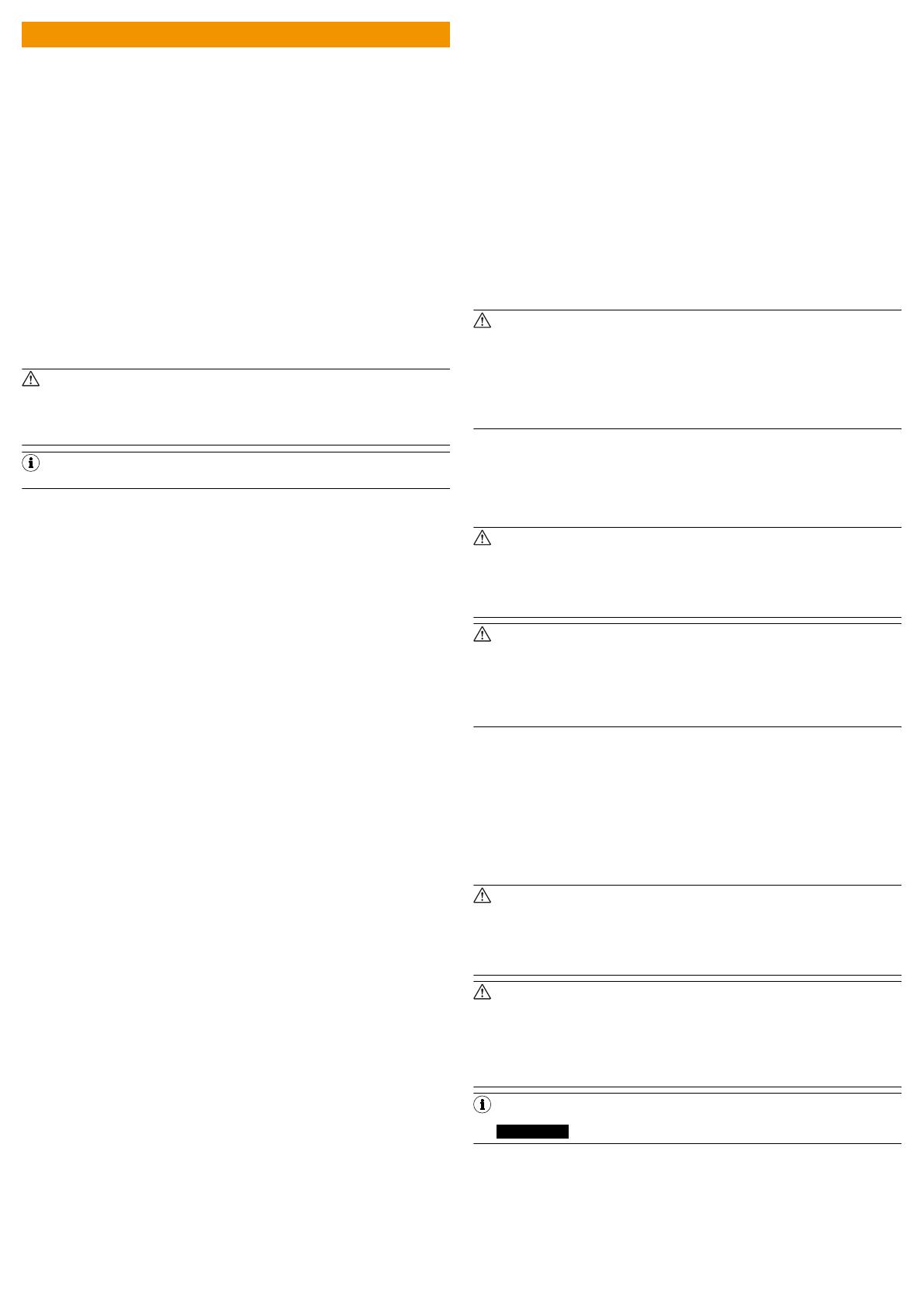
N O T I C E D ’ I N S T R U C T I O N f r
1 À propos de ce document
Veuillez lire attentivement cette notice d’instruction avant de travailler avec le
système de Feedback-moteur fiable, de le monter, de le mettre en service ou de
procéder à sa maintenance. Le fabricant ne peut garantir la fonction de sécurité
que lors du respect des prescriptions de cette notice d’instruction.
Ce document est un document original.
1.1 Objet de ce document
Cette notice d’instruction, destinée au personnel technique qualifié du fabricant
de la machine ou de l’exploitant de la machine, constitue un guide de montage
fiable, d’installation électrique, de mise en service, ainsi que de fonctionnement
et de maintenance du système Feedback-moteurfiable .
Cette notice d’instruction doit être accessible à toute personne utilisant le
système Feedback-moteur fiable.
En outre, la planification et la mise en œuvre de capteurs de sécurité, tels que le
système Feedback-moteur fiable, requièrent des compétences techniques que ce
document ne procure pas.
Il est fondamental de respecter les prescriptions réglementaires, légales et
concernant la sécurité lors du montage et du fonctionnement du système Feed‐
back-moteur fiable.
1.2 Symboles et conventions documentaires
AVERTISSEMENT
La consigne de sécurité vous indique des prescriptions concrètes pour le
montage et l’installation sûrs du système Feedback-moteur fiable. Il doit
prévenir les accidents. Lisez et suivez attentivement ces consignes de
sécurité !
REMARQUE
Indique la présence d’astuces et recommandations utiles.
b
Elles sont signalées par une flèche. Lisez et suivez attentivement les instruc‐
tions.
1.3 Documents annexes
•
Information technique « HIPERFACE DSL
®
Safety », référence 8017596, ver‐
sion de 02/2017 (ou plus récente)
•
Livre blanc "Supplementary notes for EES/EEM37 Motor feedback systems",
référence 8021843, version de 10.2017 (ou plus récente)
2 Pour votre sécurité
Ce chapitre est destiné à votre sécurité et à celle de l’utilisateur de l’installation.
2.1 Consignes de sécurité générales
Pour le montage et l’utilisation du système Feedback-moteur fiable ainsi que pour
sa mise en service et les contrôles techniques réguliers, il est impératif d’appli‐
quer les prescriptions légales nationales et internationales, notamment :
•
Directive machines 2006/42/CE
•
Directive d’utilisation des outils de travail 2009/104/CE
•
Les prescriptions de prévention des accidents et les règlements de sécurité
•
toutes les prescriptions de sécurité importantes.
Le fabricant et l’opérateur de la machine sur laquelle le système Feedback-
moteur fiable va être mis en œuvre sont responsables vis-à-vis des autorités de
l’application stricte de l’ensemble des prescriptions et règlements de sécurité en
vigueur.
Le fabricant du système d’entraînement relié doit, lors du dimensionnement du
système d’entraînement, satisfaire aux exigences de sécurité, décrites dans
l’implémentation « HIPERFACE DSL
®
Safety ».
2.2 Utilisation conforme
Le système Feedback-moteur, en raison de son équipement, est prédestiné au
fonctionnement dynamique et précis des circuits de régulation avec boucle
d’asservissement.
Le système complet, constitué d’un codeur, d’un système d’analyse, d’un servo-
convertisseur et d’un moteur, forme un circuit de régulation.
L’utilisation sécurisée de systèmes Feedback-moteur fiables avec interface HIPER‐
FACE DSL
®
se réfère à l’utilisation en liaison avec des systèmes d’asservissement
qui fonctionnent avec des moteurs synchrones AC triphasés ainsi qu’alternative‐
ment sur des moteurs asynchrones AC.
Les informations suivantes peuvent être déduites des signaux de position
numériques du système Feedback-moteur directement couplé sur l’arbre moteur.
•
chez les moteurs synchrones AC, il s’agit des informations sur les tours ou la
vitesse ainsi que l’information de commutation.
•
chez les moteurs asynchrones, il s’agit des informations sur les tours ou la
vitesse.
Le système Feedback-moteur fiable, en combinaison avec un système
d’entraînement selon CEI 61800-5-2, peut être utilisé dans des applications de
sécurité jusqu’à la catégorie 3 et PL d selon EN ISO 13849 ou niveau d’intégrité
de la sécurité CL3 selon EN 62061 .
Le niveau d’intégrité de sécurité du codeur est SIL2. SC 3 est la fonction
systématique du codeur. Uniquement implémenté dans l’architecture redondante,
le codeur peut être utilisé dans les applications SIL3, à défaut en cas d’utilisation
autonome, il est employé jusqu’aux applications SIL2.
Il satisfait aux exigences de la directive machine 2006/42/CE et assiste le
système d’entraînement en matière de garantie :
•
Des fonctions de sécurité qui se basent sur l’information de position absolue
sûre ou l’information de position incrémentale du système Feedback-moteur.
Les fonctions de sécurité ne s’appliquent que pour une seule rotation du
moteur (simple tour).
•
Pour des fonctions de sécurité qui se basent sur la position absolue multi‐
tours sûre, lors du démarrage, le système Feedback-moteur ne fournit qu’un
canal sans diagnostic de sécurité. Un second canal doit être réalisé par l’uti‐
lisateur à l’aide d’autres mesures. Ce second canal peut être mis à disposi‐
tion par l’utilisateur en enregistrant la position du système Feedback-moteur
avant l’extinction et en la comparant avec la position de démarrage du
système Feedback-moteur lors du prochain démarrage. Ce n’est que lorsque
les valeurs sont totalement identiques que la position absolue multitours
peut être utilisée de manière sécurisée. Autrement, l’utilisateur doit
procéder à une course de référence. Sans un second canal pour la position
absolue multitours, il faut exécuter une course de référence lors de chaque
démarrage du système Feedback-moteur afin de confirmer la position abso‐
lue.
Le système Feedback-moteur n’est pas en mesure d’instaurer un état sûr du
système d’entraînement de manière autonome. Le système d’entraînement doit
instaurer l’état sûr sous forme de réaction à une erreur affichée du système Feed‐
back-moteur.
AVERTISSEMENT
Le système Feedback-moteur fiable ne doit être utilisé uniquement dans les
limites des caractéristiques techniques, dimensions et tolérances et des
conditions d’exploitation prescrites et spécifiées ; il faut respecter les couples
de serrage indiqués.
Pour toute autre utilisation, aussi bien que pour les modifications, y compris
concernant le montage et l’installation, la société SICK STEGMANN GmbH
décline toute responsabilité.
2.3 Utilisation non conforme
Le système Feedback-moteur doit être monté et calibré précisément selon les
prescriptions des instructions d’installation. Toute installation ou calibrage incor‐
rects du codeur peut entraver les fonctions et données spécifiées, une restriction
partielle ou une panne totale des fonctions de sécurité spécifiées ne pourra pas
être exclue pour certains cas.
AVERTISSEMENT
S’il est impossible d’exclure de façon fiable des excitations dans l’application
près des fréquences de résonance (point de résonance > 1 100 Hz) , il faut
réaliser des tests adaptés de l’ensemble du système d’entraînement lors de
la première mise en service de l’installation. Des mesures correctives
adaptées doivent être intégrées.
AVERTISSEMENT
Près des fréquences de résonance, des violations de la précision spécifiée de
la valeur de position peuvent survenir. Lors d’une très grande amplitude de
l’excitation mécanique près des fréquences de résonance, une perturbation
ou une panne des fonctions de sécurité spécifiées peuvent se produire. Nous
recommandons de limiter le fonctionnement près des fréquences de
résonance ou du moins de limiter l’amplitude.
2.4 Exigences relatives aux qualifications du personnel
Seul le personnel qualifié est habilité à procéder au montage, à la mise en ser‐
vice, au contrôle, à la maintenance et à l’utilisation du système Feedback-moteur
fiable. Les personnes qualifiées sont celles qui
•
disposent d’une formation technique appropriée,
•
ont reçu une formation relative à la commande et aux directives de sécurité
en vigueur par l’exploitant de la machine, et
•
ont accès à cette notice d’instruction.
3 Étude de projet
AVERTISSEMENT
La tension d’alimentation doit être générée depuis des systèmes PELV (EN
50178). Le système Feedback-moteur correspond à la classe de protection III
selon DIN EN 61140. Si la tension d’alimentation n’est pas générée depuis
des systèmes PELV, l’utilisateur doit prendre d’autres mesures assurant une
isolation sûre des pièces conductrices de tension réseau.
AVERTISSEMENT
N’utiliser que des capteurs de température avec une isolation double ou ren‐
forcée, car il n’y a pas d’isolation galvanique du capteur de température dans
le système Feedback-moteur.
Le courant du bloc d’alimentation secteur qui alimente le système Feedback-
moteur doit être limité en externe à 1 A max. ; soit au niveau du bloc d’ali‐
mentation même, soit par un fusible.
REMARQUE
Lors de la conception du courant de mise sous tension, respecter les
illustration 1 !
8021265/17O7/2020-03-31/de, en, es, fr, it EES37-2... EEM37-2...
| SICK
13